One of the most troubling and disheartening things about embroidery is when a piece fails. We've all experienced it -- we spend money on fabric, designs, and materials; time setting up and embroidering the design; and at the end of all that, we're left with an embroidered piece that has gapping, shifting, or spaces in the embroidery.
Don't give up and throw your machine out the window. There are four main causes to gapping (also called "poor registration"), and they're all easily fixed with a little time, materials, and ingenuity.
Here are the main causes of poor registration that I'll discuss in greater detail below:
1. Stabilizer and fabric mismatch;
2. Fabric slipping in the hoop (or fabric not hooped);
3. Too-tight bobbin tension;
4. Hoop obstruction.
First, stabilizer and fabric mismatch. If there is too much or too little stabilizer, or the wrong kind, then chances are, you'll have problems.
When manufacturers make fabric, they don't know that we'll be using it as a canvas for our embroidery. That's why we need stabilizer -- to support and "stabilize" the fabric for the extra stitches that we add to it.
Here's an example from Jackie, an embroiderer who stitched a patriotic panel scene onto felt, with no stabilizer. The image on the left is Jackie's, and you can see how there's significant gapping in the area where the bush on the left is to meet the house. Also, notice how the shading on the roof is looking a bit straggly, and not very crisp. Finally, see how the bottom right section is 1/4 inch out of alignment with the design.
Jackie's idea of not using stabilizer with her fabric choice didn't work because of the physics of embroidery. As each stitch is made, the fibers of the fabric are pulled every which way -- up, down, left, and right. The fabric didn't have any stabilizer to hold it in place, so it stretched under the weight and tension of the stitches, resulting in gapping and shifting.
The example on the right shows the the results on the same fabric (felt) with cutaway. The cutaway stabilizer does a great job holding the fabric nice and even during the embroidery, and the results are perfect.
That's an example of how a piece can fail if no stabilizer is used. Now let's take a look at how a piece fails when the wrong kind of stabilizer is used. Embroiderer Agnes was having problems with her Sheltie design. She was using a fabric that was a little heavier than linen, with tear-away stabilizer.
Note the gapping in the back foot area, how it's separating from the leg. Also, stitches appear to be missing in the dog's left ear. Compare that to the stitchout on the right, which was on fabric backed with cutaway stabilizer.
The piece on the left failed because the wrong kind of stabilizer was used. When working with wildlife or animal designs, designs that are complex with solid fills, cutaway stabilizer is going to do the best job. Because wildlife designs have a lot of stitches for the layering and shading, the needle is perforating the fabric and stabilizer over-and-over-and-over again in the same spots as you embroider the design.
With each needle perforation, the tear-away stabilizer gets weaker and weaker until nothing is left to support the fabric. That leaves the fabric fibers free to shift and move around -- thus the rear leg separated from the body. It also means that stitches are going to land on top of each other rather than next to each other. See the gap in the upper ear? The stitches are actually there -- but they look like they're missing because they landed in the wrong place! You'll note puckering in Agnes's piece, which is also caused by tear-away stabilizer. More about that can be found in the article All Puckered Out, which you can find by clicking here.
There are many, many different brands of stabilizer on the market today -- so much that it can be a little overwhelming when trying to find the right one. Please feel free to use my stabilizer and matching guide, which you can find by clicking here.
It's also worth mentioning that using too much stabilizer can also cause gapping. Some folks use two pieces of cutaway, or two pieces of tear-away, or one of each to make sure they have all their bases covered. That will also cause gapping -- the needle working through so many layers gets dull pretty fast, which means that it moves the fibers around more and more with each perforation. The layers of fabric and stabilizer shift, and you'll see gaps in the stitchout.
Second, hooping. Not hooping, or not hooping tightly enough, can result in gapping. I mentioned before about how stitches add weight to a piece of fabric, and how stabilizer helps to support the fabric. The hoop serves a similar purpose.
As each stitch is made on the fabric, the fabric's physical reaction is to contract under the weight and tension of the thread. The hoop's purpose is to counteract that natural, physical reaction, and keep the fabric nice and even. If you're hooping the stabilizer, but not the fabric, then you may see gapping and shifting.

Take a look at this example:
We embroidered two sweatshirts with the same design -- one sweatshirt was hooped with stabilizer, and one was stitched with the stabilizer hooped and the sweatshirt adhered to the stabilizer with temporary adhesive.
Sections of the sweatshirt are side by side to the left. Note how the unhooped sweatshirt has less coverage (the blue sweatshirt is peeking through) and how there's a gap in the hat. Now, this is a minor problem, and if someone is standing 4 feet away they won't be able to tell, but if you're like me, you want your embroidery to look great!
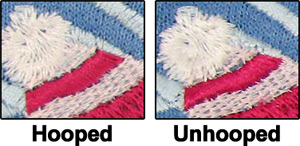
Here's another section of the sweatshirt showing similar gapping, and fuzzy stitches. Remember that the fabric wants to contract and pull together under the stitches, and hoop's job is to counteract that, and hold the fabric nice and tight.
I know a lot of embroiderers don't want to hoop the fabric, for a variety of reasons. Maybe the fabric is hard to hoop (like thick and thirsty bath towels), or they don't want to wash the item to remove the mark left by the hoop. I understand -- really I do! I struggle with hooping towels too, it usually takes me 2 - 3 tries to get it in the hoop with the stabilizer. But to get the best results, hoop as much as possible.
Also, keep in mind that even if you hoop everything, your hoop has weak spots. If you have a rectangular hoop, the weak spot is the lower left corner. If the fabric is hooped loosely, or slipping in the hoop, you're most likely to find the problem in that area.
Embroiderer Anne Campbell wrote an excellent article about reinforcing the weak areas of the hoop -- click here to find it. And, many embroiderers have submitted tips that help with hooping, from using foam pencil grips on the screw to using rubberized shelf liner to using rubber bands and double-sided tape to make sure that fabric is hooped firmly. Click here to find those tips. The ideas that have been sent in are wonderful!
Third, bobbin tension troubles. This is most common when working with designs that have outlines, but I've also seen examples with complex designs that have solid fills.
If you're stitching designs that have a thin outline, and your outline is separating from the main part of the design; and if you are 100% sure that you're using the right fabric and stabilizer combination, then try loosing your bobbin tension just a bit. If your bobbin tension is a little too tight, that's going to pull the stitches down, and the fabric fibers out, and that'll cause your outline to be off.
If you're working with a design that has solid fills adjacent to each other, and you're finding that there's a slight separation between the fills, that's an indication that your bobbin tension is a little too tight.
Please note that in order for a bobbin to cause gapping in an embroidered piece, the tension would need to be dramatically off, and you'd probably notice that problem in other areas, too. It may be time to take the machine in for service, and ask the tech to check the bobbin tension.
One good way to see if your bobbin tension is right is to stitch a design that has a satin column -- small letters are good choices. Flip the piece over and look at the backside. If you see that 1/3 to 1/2 of the stitches in the satin column are bobbin stitches, then that bobbin tension is right.
Fourth, hoop obstruction. This is unusual, but worth mentioning. A few months ago an embroiderer contacted us -- she was having problems with sections of the design being out of place. She was using a sturdy fabric with cutaway stabilizer, and we worked with her for several days trying to find the problem.
She finally found the problem -- a tissue box had fallen behind the machine, and the hoop was hitting it as it was moving around! That caused the stitches to be out of alignment. It's worth noting that before beginning a project, check to make sure that your work space is free of anything that could restrict the hoop's movement.
And, if you have little critters in your home, keep a close eye on them when you're working! We've received some adorable photos that gave us "paws." We know that we wouldn't be inspired without our little kitties Rocco, Trixie, and Natasha helping us in our sewing room, but do make sure that your felines are well out of the way in order to avoid a "catastrophe."