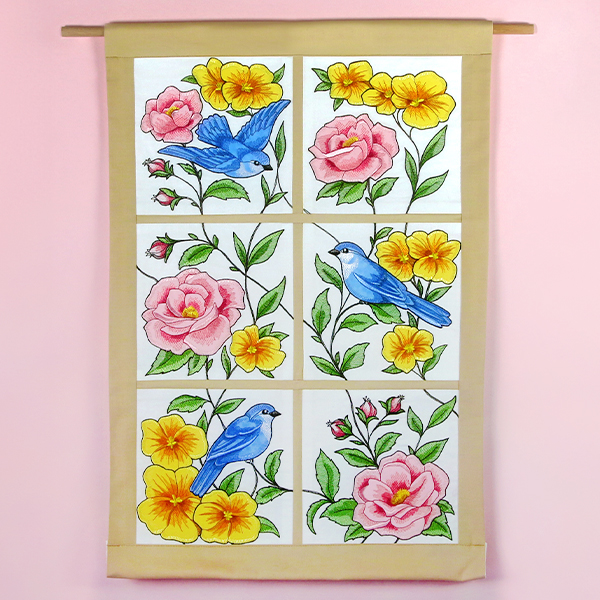
Create your own hanging mini quilt using our six-panel applique scene design packs! Project instructions below will walk you through the process and show you how to make your own.
Supplies
- Cotton fabric
- Small bits of fabric
- Scissors
- Temporary spray adhesive
- Ruler
- Rotary cutter
- Wooden dowel
- Cutaway stabilizer
Designs Used
When you download each applique panel design, you will find multiple files. One is an embroidery file, and the other are dieline files marked with the letters "DL". Dielines are used to cut the fabric to the correct shape and size.
Open and print each dieline file using embroidery software. If you do not have embroidery software, take a look at our helpful video on using dielines without software. We also recommend Wilcom's Hatch software which comes in different levels depending on what you'd like to use the software for. Hatch Organizer works well to view your designs, print dielines and templates, change design colors, and create basic design layouts. (this is an affiliate link - we may earn a commission off purchases made with this link)
First, spray the back side of the paper dieline with temporary spray adhesive, and smooth it onto the right side of the fabric.
Repeat for each applique piece used in the scene.
Smooth the fabric and dieline pieces over cutaway stabilizer.
Cut out the dielines.
To start the panel scenes, begin by spraying a piece of cut away stabilizer. Smooth a piece of cotton fabric in place.
Hoop the stabilizer and cotton fabric.
Attach the hoop to the machine and follow the color change sheet to embroider the design.
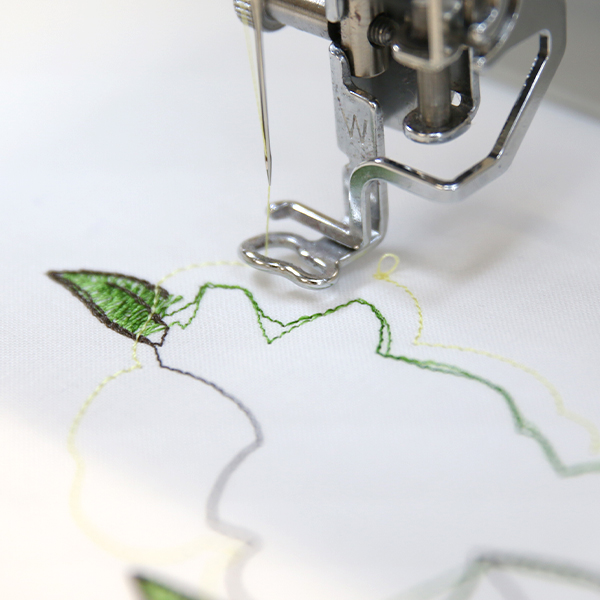
Continue to follow the color change sheet, stop after you've sewn out the first dieline.
After the first dieline has sewn out remove the hoop from the machine, but do not unhoop the design. Spray the wrong side of the first fabric piece with temporary spray adhesive. Place the fabric on the stabilizer inside of the sewn dieline.
Then place the hoop back onto the machine, and embroider the tackdown for the previously placed fabric piece. A tackdown holds the fabric in place for the remainder of the design.
Follow the color change sheet, and stop once again after the next dieline outline finishes embroidering. Repeat to remove the hoop from the machine, do not unhoop the stabilizer, and again place the next applique piece.
Return the machine and continue to follow the color change sheet. Placing each fabric piece in their dieline as the design sews out. Each applique scene will be different, so look at the color change sheet carefully.
Once all the embroidery has finished, unhoop the embroidery design and stabilizer. Set it aside. Do not trim the excess fabric and stabilizer yet.
Repeat the previous steps to embroider all of the designs you will be using.
To begin assembly, first iron one of the embroidered designs with a pressing cloth on top. Try to remove any wrinkles, and make the square shape as flat as possible.
Then cut the cotton 1/2" away from all four sides of the embroidery to create the seam allowance. The easiest way to do this is with a quilting ruler and a rotary blade. However if preferred, you can measure and draw the 1/2" seam allowance around the square with a marking tool and cut with scissors instead.
Repeat to press all of the embroidery designs so they are square and flat. Then cut them out leaving the 1/2" seam allowance around every side of all designs.
The width of the sashing is up to you, in this example we wanted to have 1/2" sashing between the internal panels. We'll also still be keeping a 1/2" seam allowance.
Planning out how many of each sashing width you need is easy. Nothing needs to be cut to an exact length, as we will be trimming the size as we go. Our embroidery designs are just under 8" wide and tall. Rounding them up to 8" makes the math easier.
For best results, add 3" - 5" to the length of each fabric strip (not the width). This helps account for seam allowance and adds some flexibility while you are working. Always cut the sashing to be longer than you need to be extra cautious.
You will need:
-3 pieces longer than 8" for the Vertical inner sashing.
-2 pieces longer than 18" for the inner horizontal sashing.
Now that you have all the embroidery designs in internal sashing cut out and ready, lay your embroidery design out to make sure you know what order you want them to be in. It can be helpful to take a picture of this before continuing to make sure you sew the right ones together, and don't get them mixed up.
Take the upper left embroidery design and one of the shorter inner sashing pieces. This would be one of the pieces that's just over 8" long.
Line up the edges of the embroidery and sashing, use pins or clips to hold in place as you sew.
The trick to perfectly lining up the seam with the edge of the embroidery is to sew with the backside of the embroidery facing up on the sewing machine. Simply sew directly on top of the outer edge of the embroidery. Sewing right on top of the stitched embroidery edge looks best and leaves no gaps. Since we cut the seam allowance to 1/2", sewing along the embroidery edge also gives us a guide to sew the correct seam allowance.
Place the pieces on the machine with the embroidery wrong side up and sew a 1/2" seam along the edge. Make sure to sew directly on top of the outer most edge of the embroidery when sewing.
After sewing, press the sashing with an iron and pressing cloth.
Then use a quilting ruler and rotary cutter to trim off the extra length of the sashing piece so it perfectly lines up with the outer edges of the embroidered fabric on both sides. Be careful to cut this straight and not crooked at all.
Take the upper right embroidery piece and lay it over the previous corner and sashing with right sides together. Lien up the edges of the right embroidery and sashing.
Pin or clip in place.
Repeat to sew the right corner to the sashing, the press nicely.
Repeat the previous steps until all rows are finished.
The horizontal sashing are sewn just like vertical sashing. To begin, take one of the longer sashing pieces, this would be one of the pieces that is just over 18" long. Pin or clip in place along bottom edge of the row for sewing.
Use a quilters ruler to trim the extra sashing away. Be sure to keep the ruler straight as you cut.
With the right sides together, line the second row with the edge of the second horizontal boarder piece.
Once again, pin or clip the sashing, and sew with a 1/2" seam allowance.
Continue to repeat the above steps to attach the second row of sashing, and the final set of panel pieces.
For the external boarder pieces cut two at 2.5 wide, we're going to use an 1 1/2" for width, with 1/2" for seam allowance.
Sew these two boarder pieces to the outer left and right sides of the panel scene and press.
With the front put together, its time to make the back piece. To do this measure your front panel. In this example ours is 17.5" wide by 22" tall.
Put the back piece over the front, with right sides together.
Pin the edges.
Sew down the sides. Like before, with 1/2" seam allowance.
Turn right side out and press.
To make the hanging channels, start by measuring a piece of fabric 9" wide by the length of your panel scene, plus 1/2" on either side. In this example ours is 19", cut two out of your fabric.
Fold the short ends of the channels in 1/2" on both sides.
Sew down the fold to hem the edges, be sure you keep it 1/2" So it fits on the edge of the panel scene.
Repeat to hem the other side as well.
Now fold in one of the long ends on both channel pieces 1/2" and press.
Take the unfolded edge and line it up with the right side of the channel against the wrong side of the design.
This fold is the hem for the front which will be tops stitched, be sure you do not have this pinned down.
Pin and sew.
Press seam flat.
Repeat these steps on the other end.
Wrap the channels around and fold.
Pin front and back pieces in place.
Top stitch the outer edge.
Press one final time to ensure that the edges are crisp and flat. Then you have a finished panel scene ready to add beauty and fun to your home!