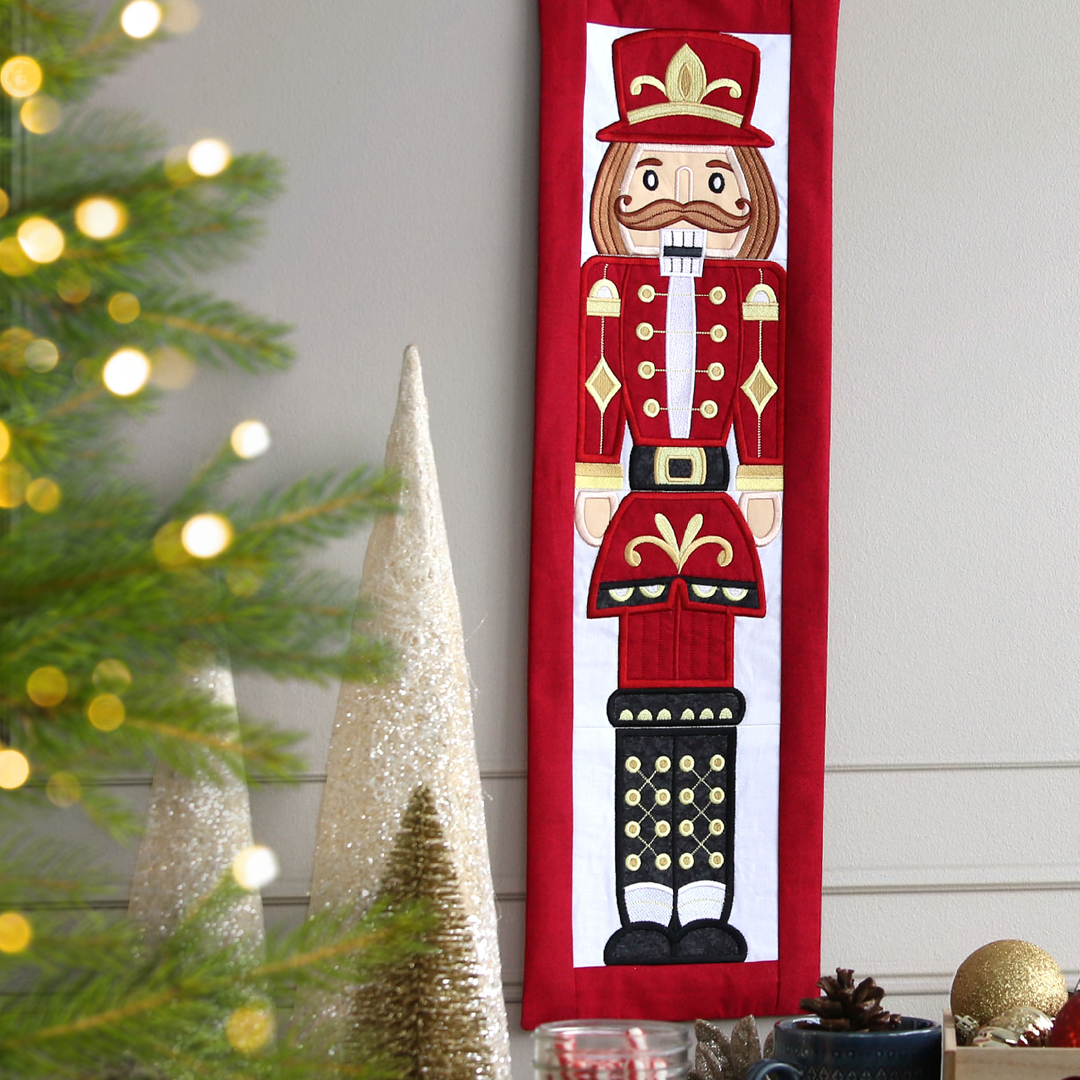
Make a beautiful panel scene with applique using this helpful tutorial!
Supplies
- Cotton fabric for embroidery
- Cotton fabric for applique
- Cotton or alternate fabric for borders and hangers
- Embroidery thread
- Temporary Spray Adhesive
- Cutaway stabilizer
Tools
- Scissors
- Sewing pins or clips
- Rotary cutter
- Cutting mat
- Fabric marking tool
- Sewing machine
- Iron
- Ironing Board
- Pressing cloth
Designs Used
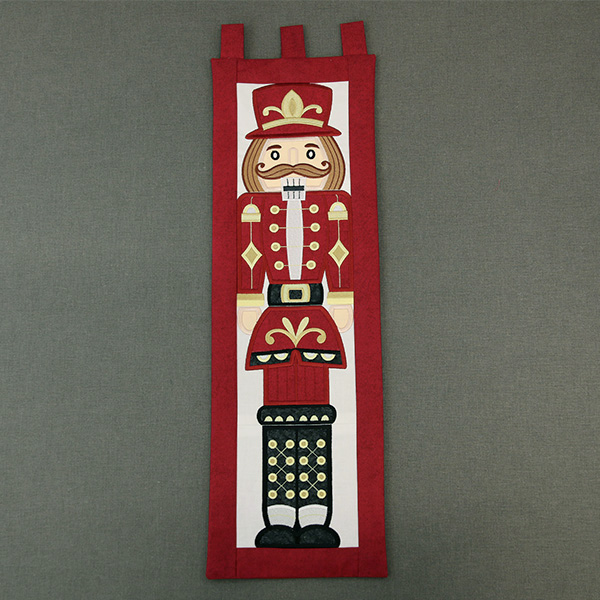
This tutorial shows how to make a wall hanging out of any of our continuous panel scenes no matter how many panels make up the scene. It will work for both square and rectangular shaped scenes, but it is meant for the panel scenes that sew the embroidered panels side by side and do not have thin fabric borders between the embroidered pieces. This tutorial also works for any hoop size of the panel scenes by simply adjusting the length you cut the borders to.
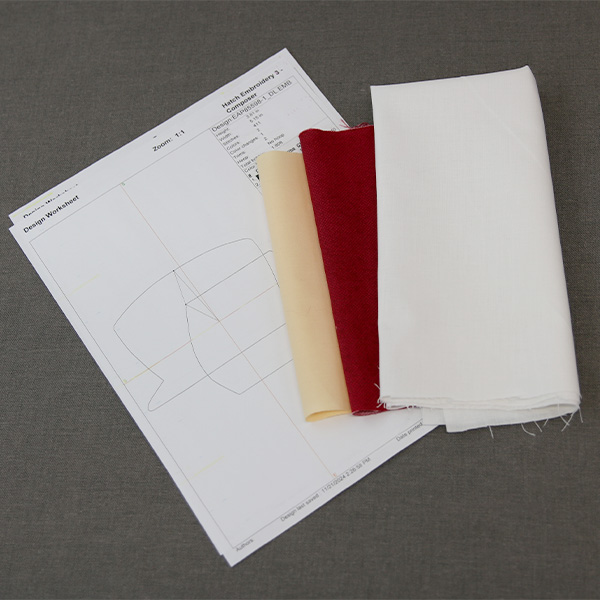
When you download the design, you will find multiple files. Some are embroidery files, and others are dieline files marked with the letters "DL". Dielines are used to cut the fabric to the correct shape and size. Open and print each dieline file using an embroidery software. If you do not have an embroidery software, take a look at our helpful video on using dielines.
We also recommend Wilcom's Hatch software which comes in different levels depending on what you'd like to use the software for. Hatch Organizer works well to view your designs, print dielines and templates, change design colors, and create basic design layouts. (This is an affiliate link. We may earn commission on purchases made with this link.)
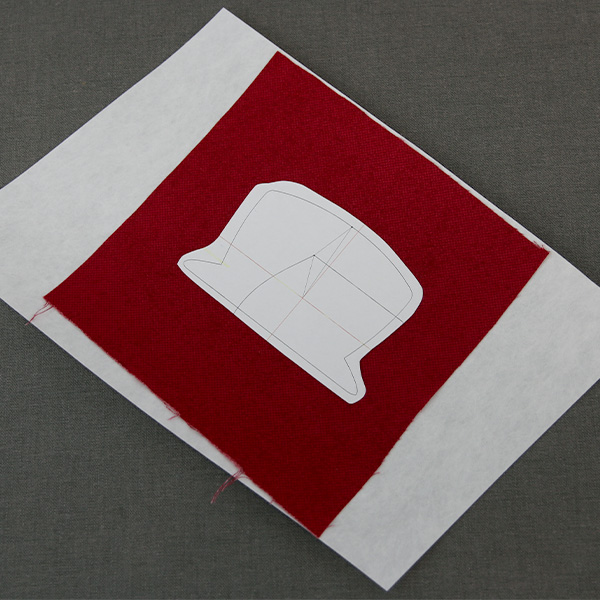
To make the applique pieces, spray a piece of cutaway stabilizer with temporary spray adhesive. Then smooth the stabilizer onto the wrong side of the fabric piece. Also spray the wrong side of the paper dieline with temporary spray adhesive, and smooth it onto the right side of the fabric.
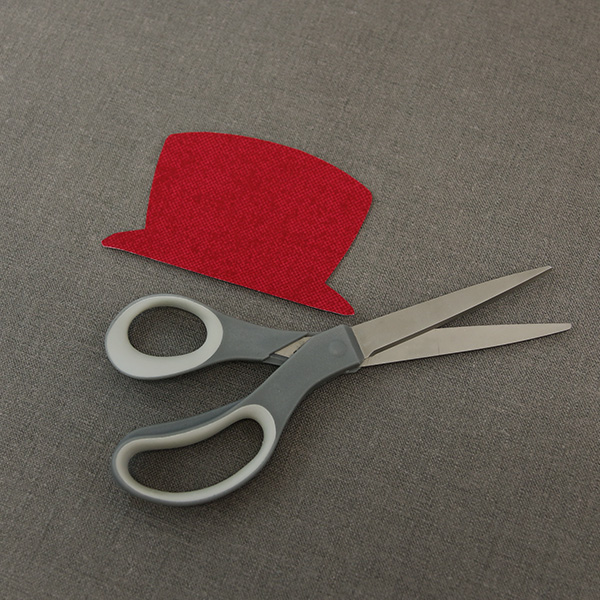
Cut the dieline shape out of the layered cotton and stabilizer. Then remove the paper dieline.
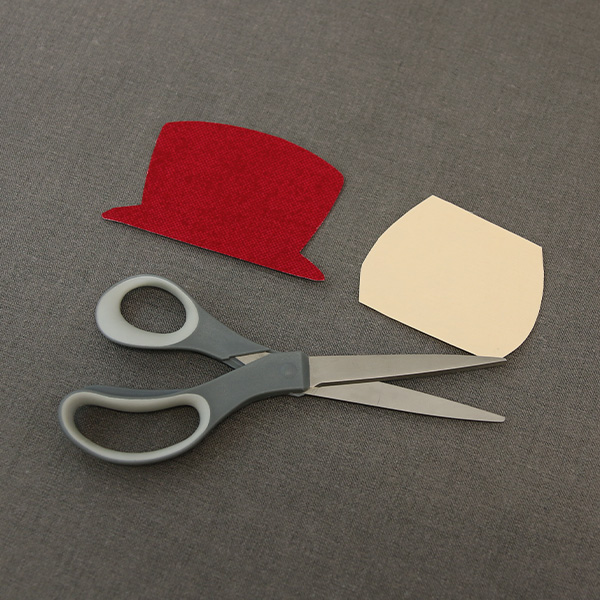
Repeat these steps to cut out all the applique pieces in the design.
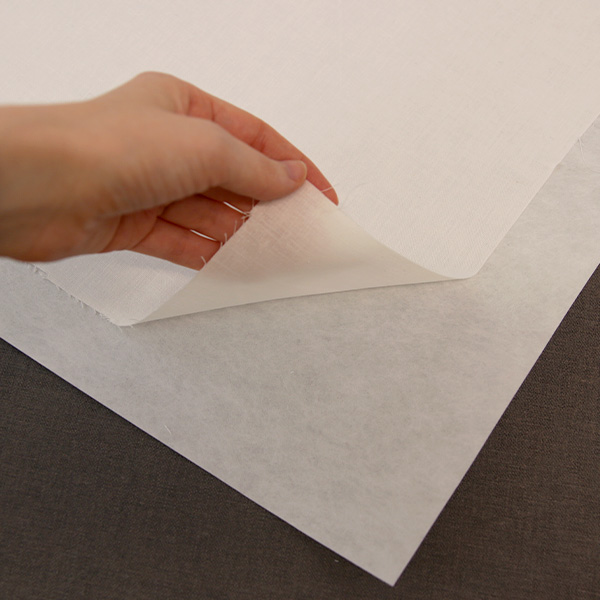
To prepare the embroidery fabric, cut a piece of medium weight cutaway stabilizer and cotton fabric (or another similar weight fabric) bigger than your hoop. Spray the cutaway stabilizer with temporary spray adhesive and smooth it onto the wrong side of the cotton piece.
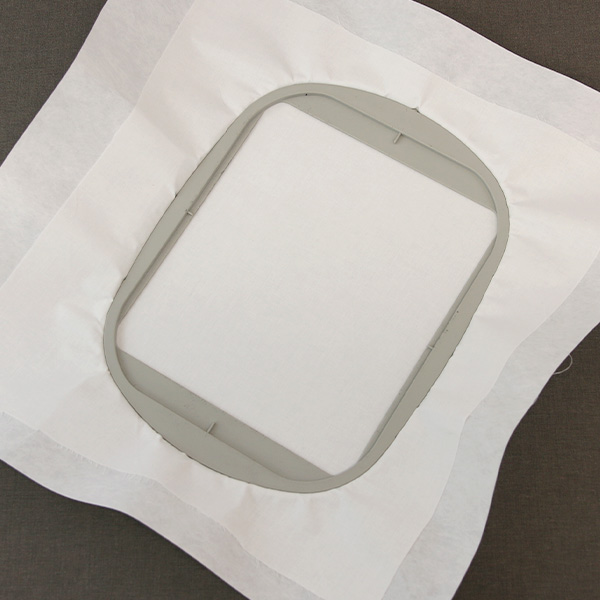
Hoop the cotton and stabilizer together. Make sure everything is hooped tightly and that there are no wrinkles or puckers in the fabric.
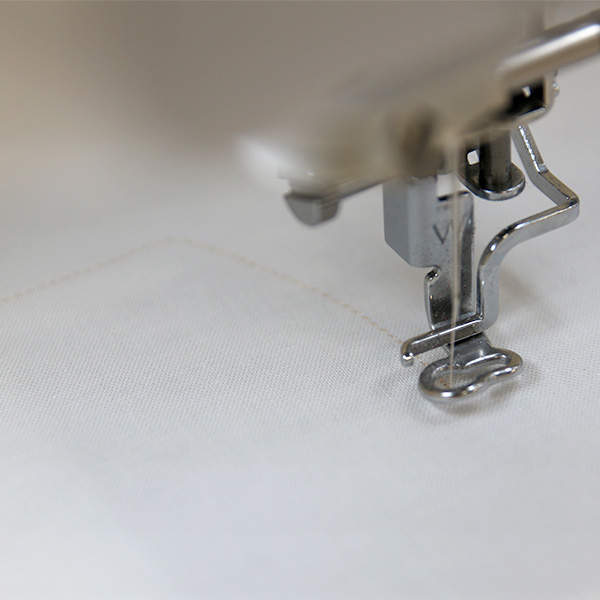
Load the first embroidery file onto the machine, attach the hoop to the machine, and begin to embroider the design.
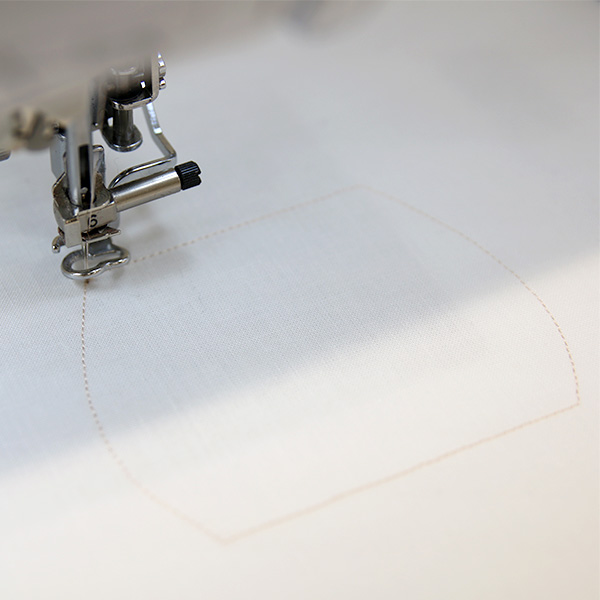
Watch the color change steps closely, and continue to embroider until you have sewn out the first step with "dieline" in the name. This dieline (or outline stitch) marks the area where the applique piece will be placed. Some designs will sew the first dieline right away, and others may have details that sew before the first dieline.
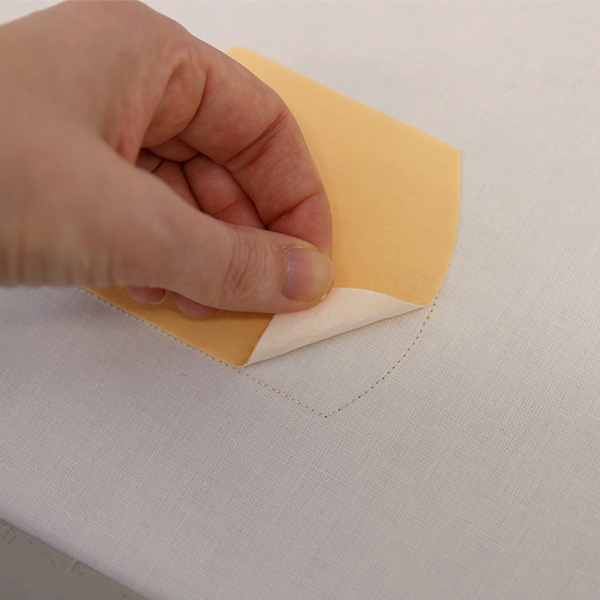
After the dieline has sewn, remove the hoop from the machine, but do not unhoop the fabric. Spray the wrong side of the first applique piece with temporary adhesive. Place the applique on the hooped fabric inside of the sewn dieline shape.
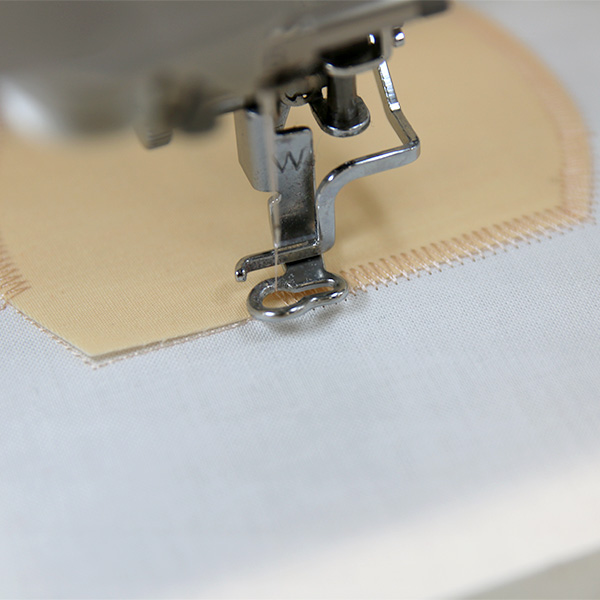
Then place the hoop back on the machine, and embroider the tackdown for the applique piece that was just placed. A tackdown holds the fabric piece in place for the remainder of the design.
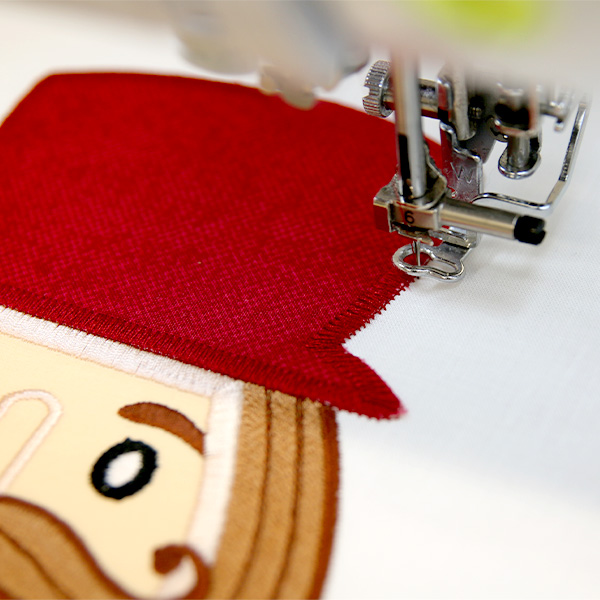
If the design has multiple applique pieces, continue to embroider the design until you get to another step labeled "dieline". Then repeat the previous steps to embroider the dieline, place the fabric piece, and embroider the tackdown.
If the design only has one applique piece, simply continue to embroider the design.
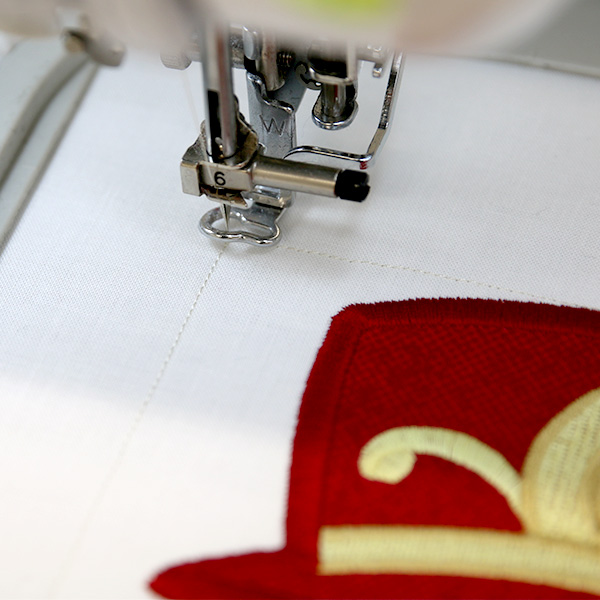
Continue to follow the color change steps, embroider all details, and pause to place every applique piece as needed. The final thing to sew will be a box around the entire design.
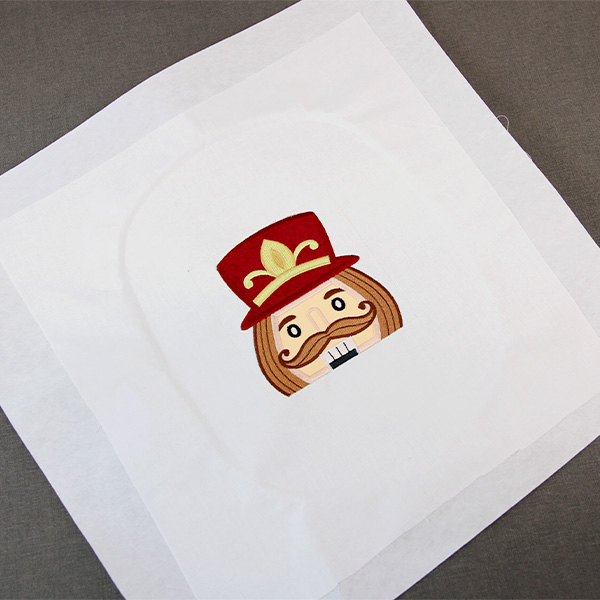
Once the embroidery has finished, unhoop the embroidered design, and set it aside. Do not trim the fabric or stabilizer yet.
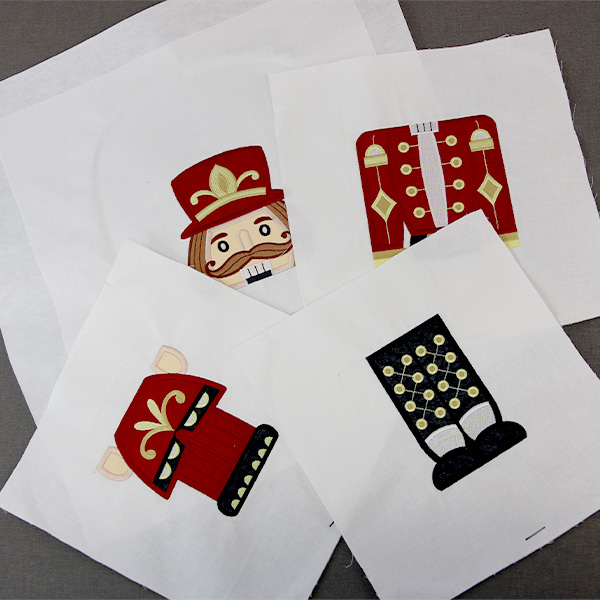
Repeat the previous steps to embroider all of the designs in the chosen panel scene. For example, the nutcracker panel scene we are making is made up of four panel embroidery files.
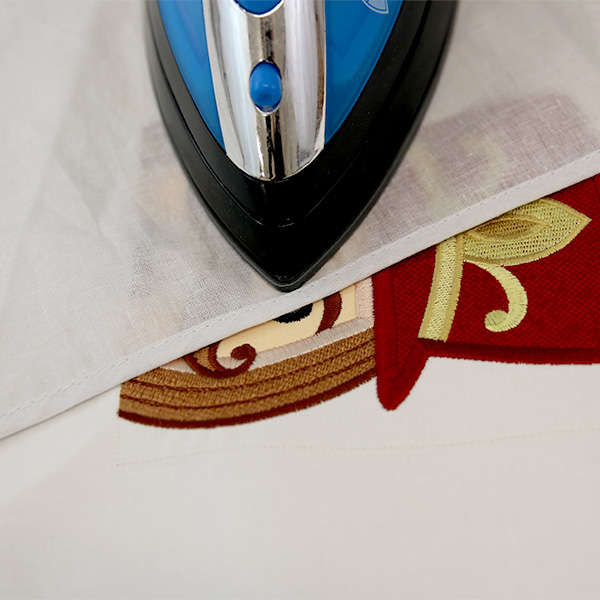
To prepare the first design panel, iron one of the embroidered panels with a pressing cloth on top. Try to remove any wrinkles, and make the sides as straight and flat as possible.
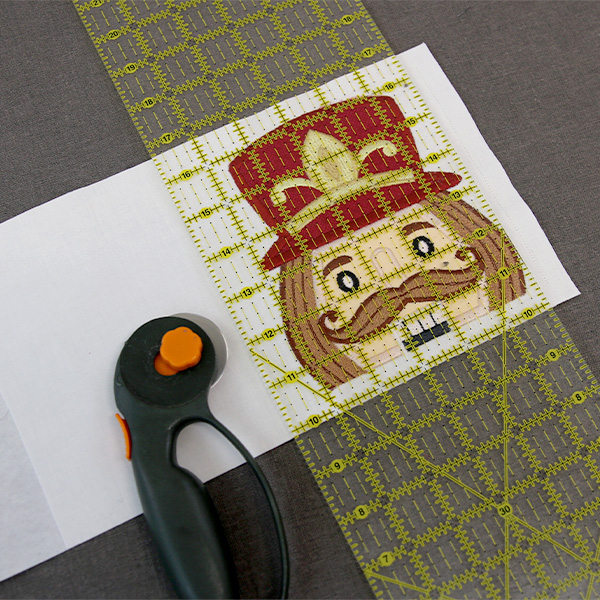
After pressing, measure 1/2in away from all four edges of the design and cut away the excess material. This will leave an even border of fabric around the edges of the embroidered design. This 1/2in border of fabric will be the seam allowance. Feel free to use whatever seam allowance measurement works best for you.
The easiest way to measure and cut the seam allowance around the design is by using a quilting ruler and rotary cutter. If preferred, you can also measure and draw the seam allowance around the outside of the panel, and simply cut on that line with a scissor instead.
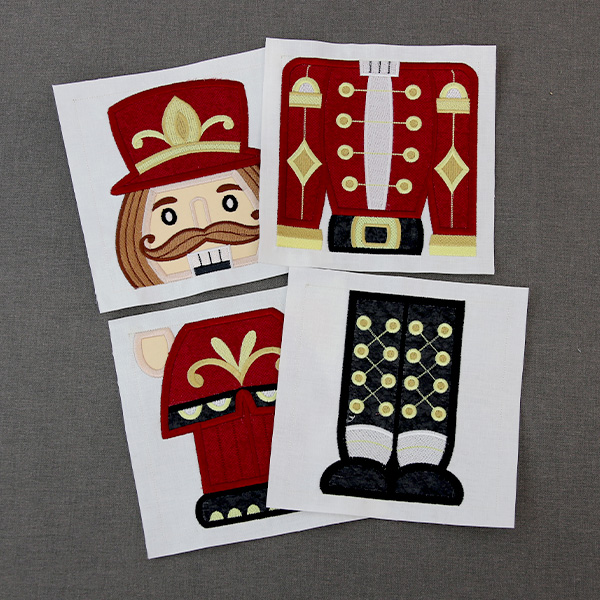
Repeat the steps to press all of the embroidery panels so they are straight and flat. Then cut them all out, leaving the seam allowance (1/2in for our example) border of fabric around all four edges of every panel.
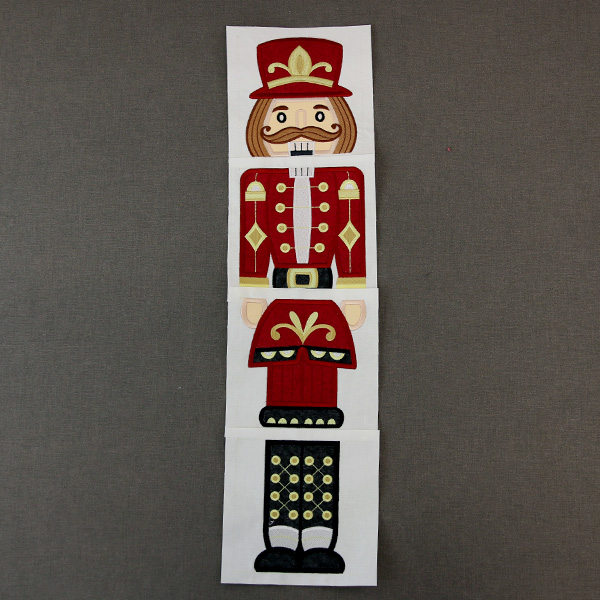
After all the panels in the scene are pressed and cut out, carefully arrange them on the work area to show which panels go next to each other when the scene is lined up. Looking at them like this while you assemble the scene will help you see which edges need to be sewn together. Keeping them arranged like this while you work will also help prevent them from being mixed up or sewn to the wrong pieces.
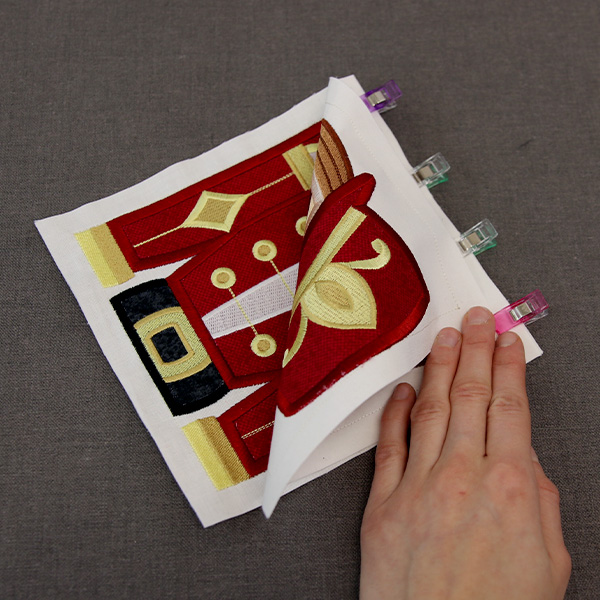
To begin assembly, take the top two squares, and lay them on top of each other with right sides together. Match up the edges of the fabric. For best alignment, carefully look between the two panel pieces and line up the outer border and corners of both embroidered panels. Then pin or clip the two panel pieces together along the side that needs to be sewn together.
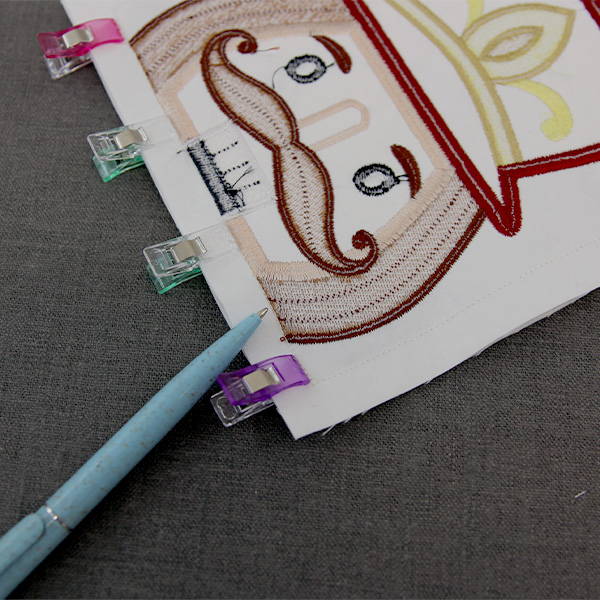
The trick to perfectly lining up your panels and seams with the edge of the embroidery is to pay close attention to the outer embroidered edge and border of the designs. When pinning any panel pieces together (like we did in the previous step), take extra care when matching up the outer borders and corners of the two panels as best you can on top of each other. The closer they are lined up, the better the panels will be aligned once sewn.
Then when sewing, you want to always sew with the backside of the embroidery facing up so you can see that outer border while you sew. Then simply sew directly on top of that outer line and edge of the embroidered design. Sewing right on top of the stitched embroidery edge will look best, and leave no gaps. Since we measured the seam allowance from this line as well, sewing along the embroidery edge also acts as a guide to sewing the correct seam allowance.
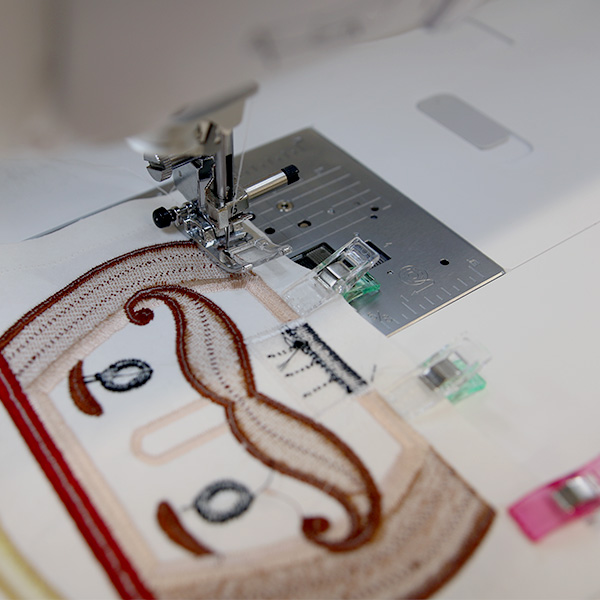
Place the pieces on the machine with the wrong side of the embroidery facing up, and sew the two pieces together with your chosen seam allowance as well as following the outer edge of the embroidered design. Make sure to sew directly on the outer most edge of the embroidery for best results.
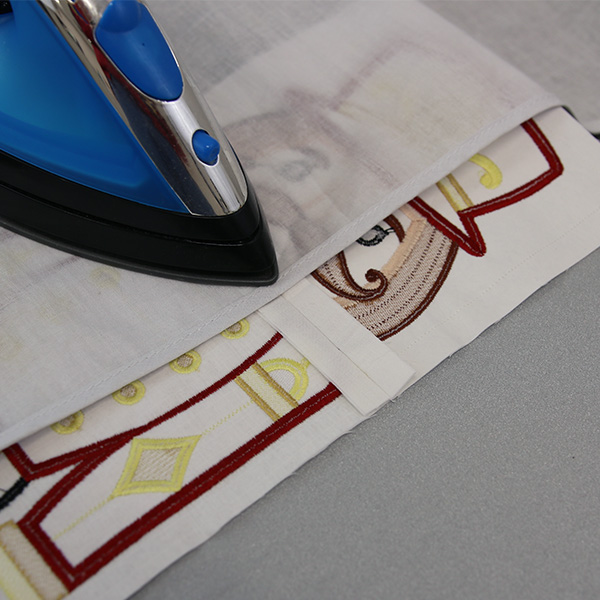
After sewing the seam, press the seam open so it lays nice and flat. Use a pressing cloth when ironing to protect the stabilizer and fabric from the iron.
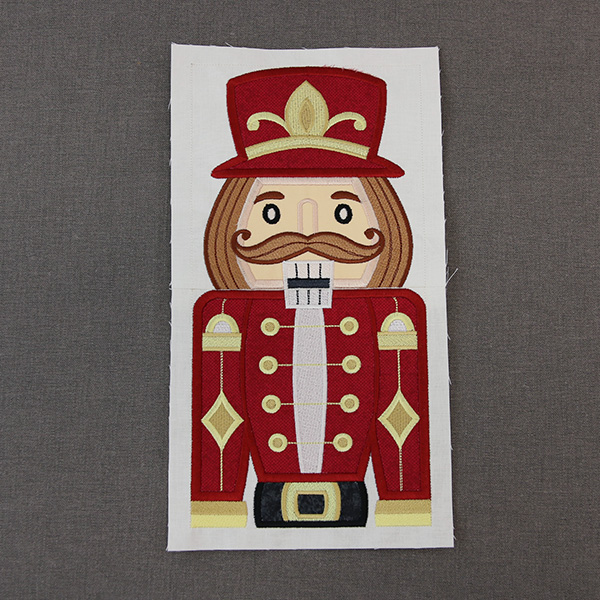
Now the top two panels are sewn together.
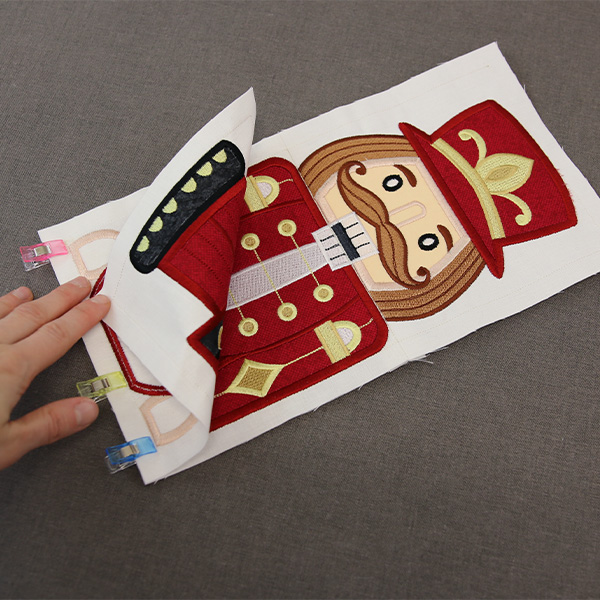
If your panel scene is a vertical scene that is just one panel wide and multiple panels tall, repeat the previous steps to pin the next panel onto the sewn pair of panels. Make sure to pin along the bottom edge where they will be sewn together.
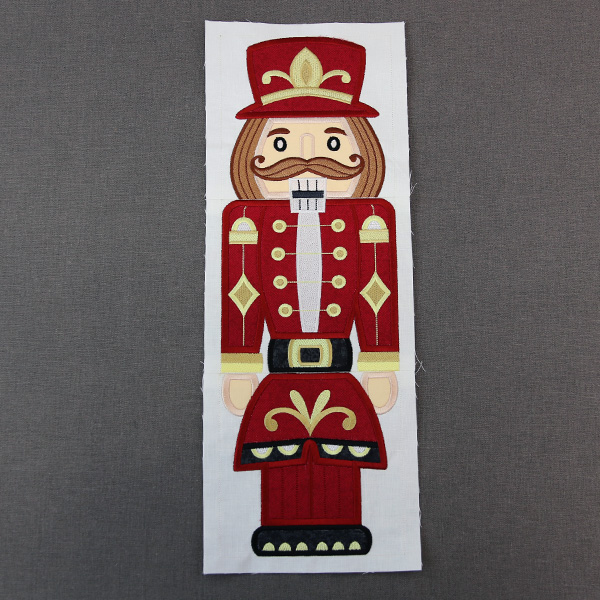
Then sew the panel on, and press open the scene.
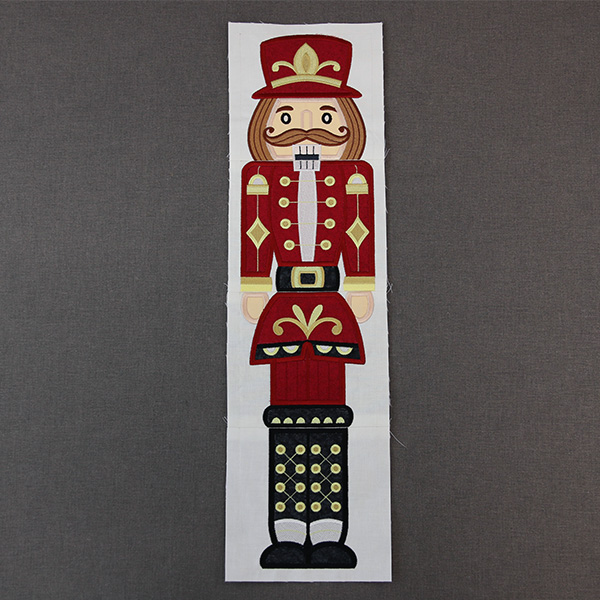
Some panel scenes have more panels than others. Repeat the previous steps to pin, sew, and press all the panels together vertically that make up the scene.
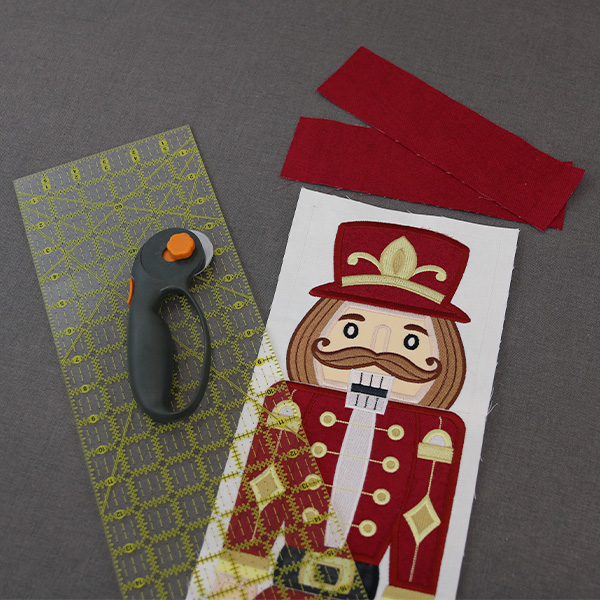
To make the top and bottom borders, we need to find the width and length to cut them to. To find the width, decide how wide you want the outer border to be on your finished wall hanging. We chose 1.50in for our desired outer border width. Then add your seam allowance to that number two times as it will have a seam along both the top and bottom edge of the border. This final number will be the width we are cutting the outer borders to. For our panel scene, we added our desired width (1.50in) + the seam allowance twice (0.50in x 2) to get a total width of 2.5in.
To find the length, measure the top edge of the assembled panel scene. Make sure to include the seam allowance visible on both sides in the measurement. Our nutcracker scene measured about 7in wide. As these panel scenes are not usually a whole number that is easy to measure on a ruler, we are going to cut the border pieces longer than they need to be. This will make the borders both easier to cut out and line up, and the excess fabric will be trimmed off after sewing.
Round up your measurement to the next whole number and then add two extra inches. For our panel scene, we rounded our measured panel width up to 7in, and then added 2in to get a total length of 9in.
Cut two outer border pieces to the width and length you found. We cut both of ours to 2.5in wide x 9in long.
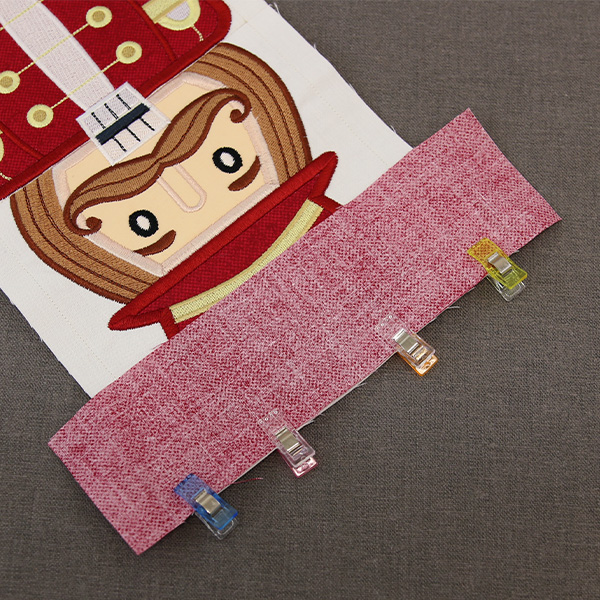
Line up the top outer border to the top edge of the panel scene with right sides together. There should be a little extra border length sticking out past both sides. Then pin or clip them together.
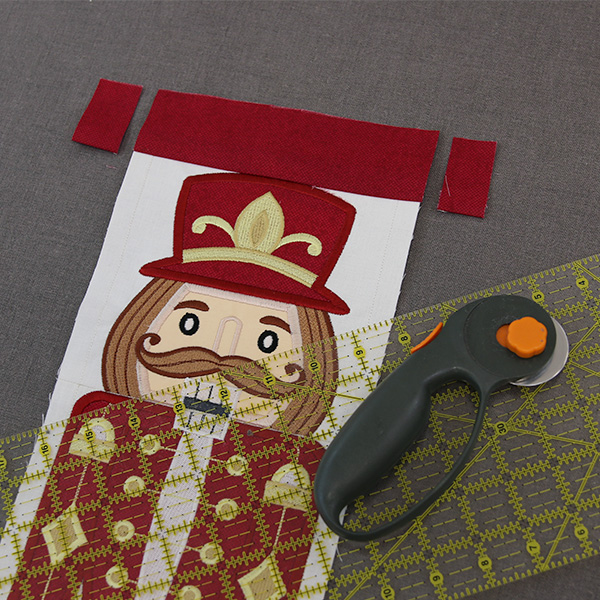
Place the pieces on the machine with the wrong side of the embroidery facing up, and sew the two pieces together with your chosen seam allowance as well as following the outer edge of the embroidered design. Make sure to sew directly on the outermost edge of the embroidery for best results.
After sewing, press the seam open so it lays flat. Use a pressing cloth when ironing to protect the stabilizer and fabric from the iron.
Then use a quilting ruler and rotary cutter to trim off the extra length of the outer border piece on both sides. Cut it so it lines up perfectly with the fabric edges of the embroidered panel pieces on both sides. Be very careful to cut the border straight. You can also use a scissor to do this if you don't have a rotary cutter, use a ruler and marking tool to draw a straight line before cutting.
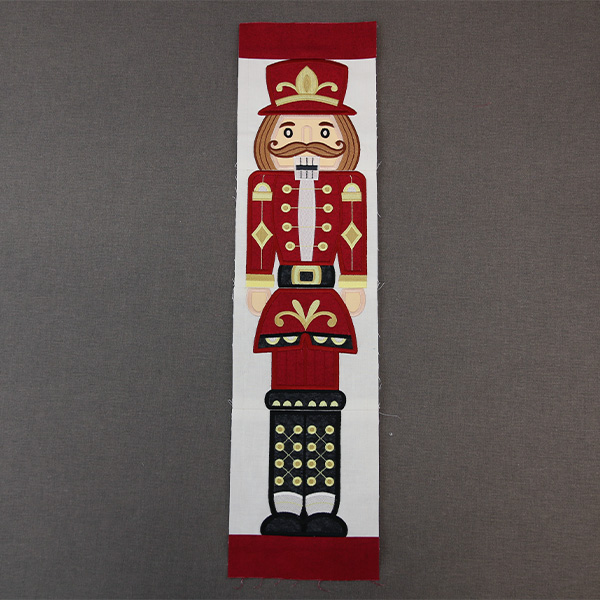
Repeat the previous steps to line up and pin the bottom outer border onto the bottom edge of the panel scene. Then sew them together, and press the seam. Then also carefully trim the extra length of the outer border piece off both sides.
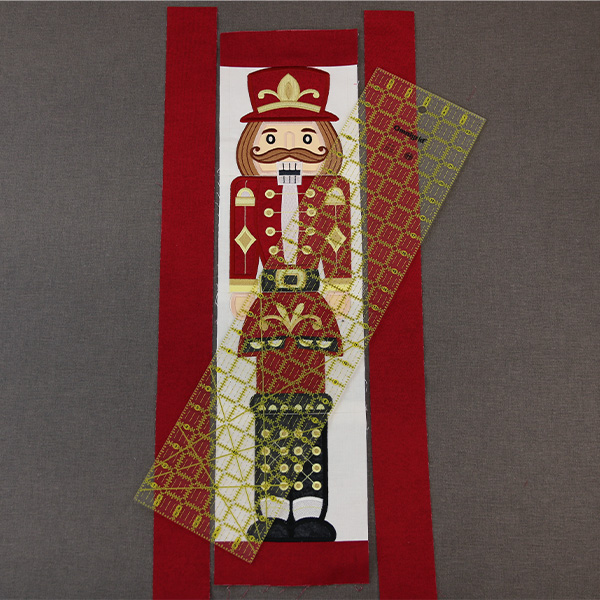
To make the two side borders, we will be using the same width as the top and bottom borders. For our panel scene, we added our desired width (1.50in) + the seam allowance twice (0.50in x 2) to get a total width of 2.5in.
To find the length, measure the left or right edge of the assembled panel scene. Make sure to include the top and bottom borders in the measurement this time. Our nutcracker scene measured about 27in tall. Round that measurement up to the nearest whole number, and then add two extra inches. For our panel scene, we rounded our measured panel width up to 27in, and then added 2in to get a total length of 29in.
Cut the two side outer border pieces to the width and length you found. We cut both of ours to 2.5in wide x 29in long.
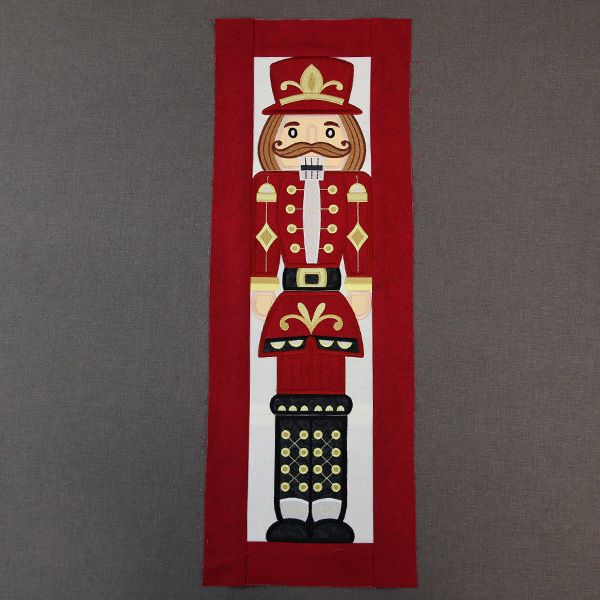
Just like we did for the top and bottom outer borders, line up the side outer borders on the left and right sides of the panel scene with the length of the borders going past the edges a little on both sides. Pin or clip them in place, sew them together, and press the seam. Then also carefully trim the extra length of the outer border piece off both sides.
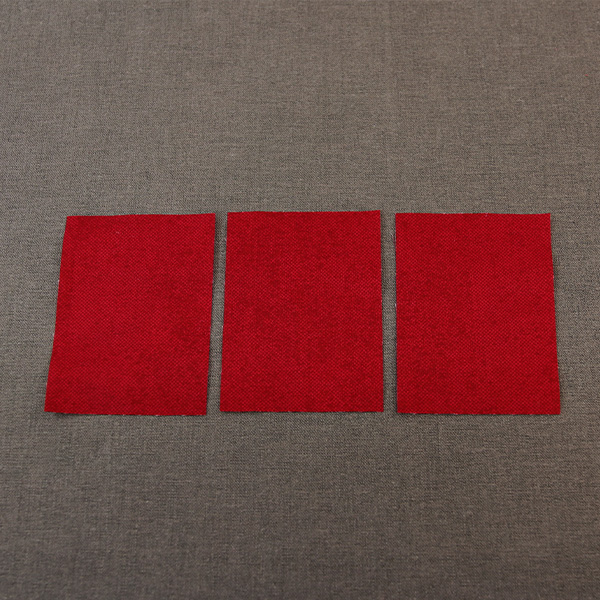
To make the hanger loops, cut three pieces of fabric that are 3.5in wide x 4.75in long. In our example, we are making these out of the same fabric as our outer borders.
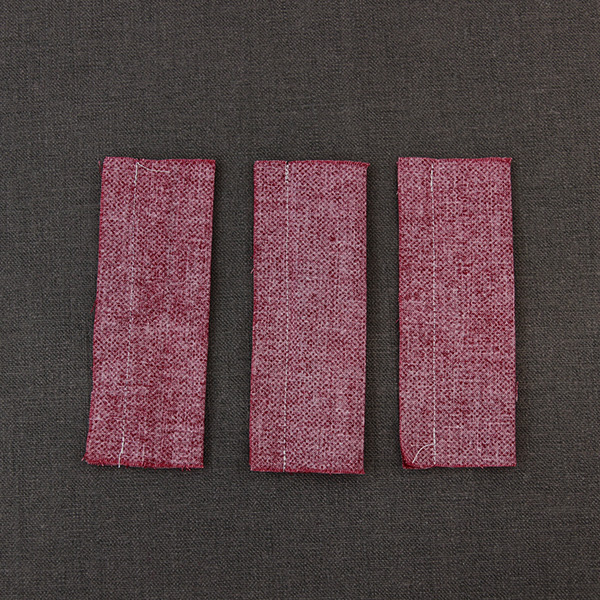
Fold the fabric pieces in half along the shorter side, and then pin or clip them along the open side. When folded they should still be 4.75in long. Sew a seam along the pinned side with a 1/2in seam allowance. Repeat for all three pieces.
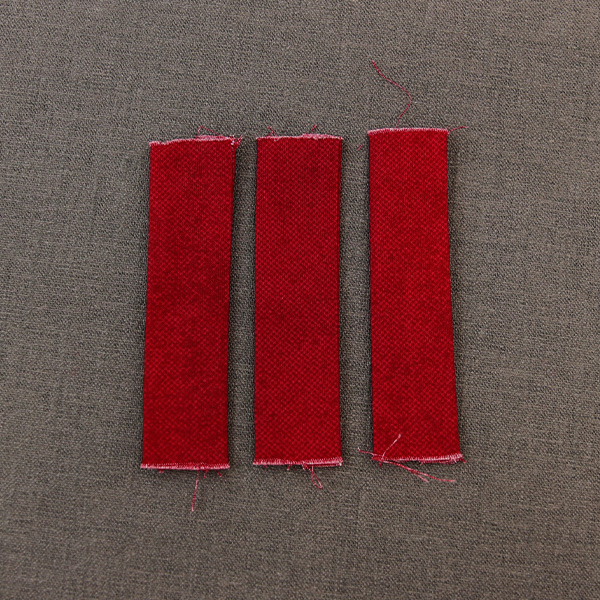
Turn the three hanger pieces right side out. Press all three hanger pieces flat with the seam on the center back of one side.
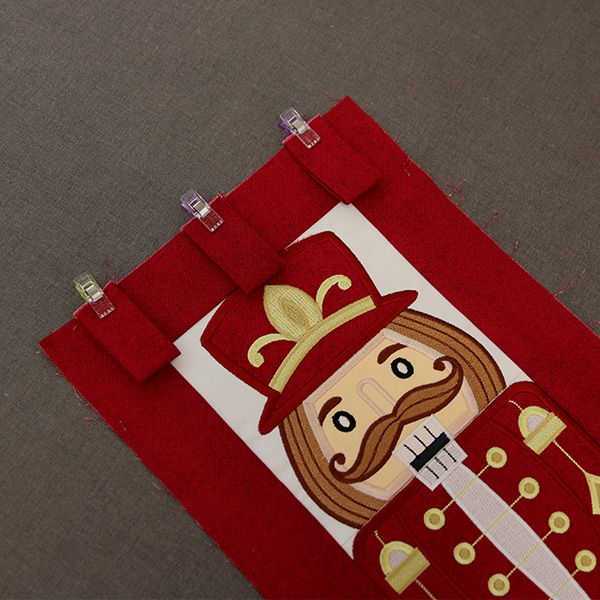
Then fold the three hangers in half again with the seam side together. Lay them along the top edge of the panel scene with the raw edge of the hangers matched up with the raw edge of the outer border.
Center one of the three hangers. Then measure and place the other two 0.75in-1.50in in from both sides. Pin or clip all three in place.
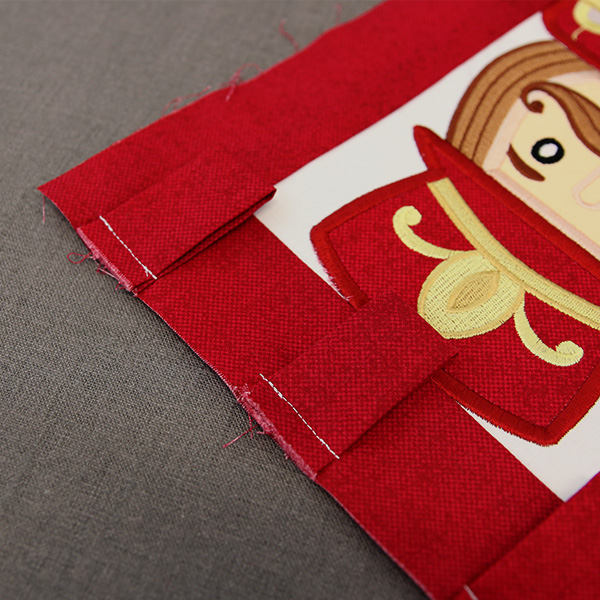
Sew a seam along the raw edge of all 3 hangers to hold them in place. For best results, sew this at a smaller seam allowance than the normal seam allowance you are using for the rest of the project, so this seam doesn't show. We sewed ours at a 1/4in seam allowance.
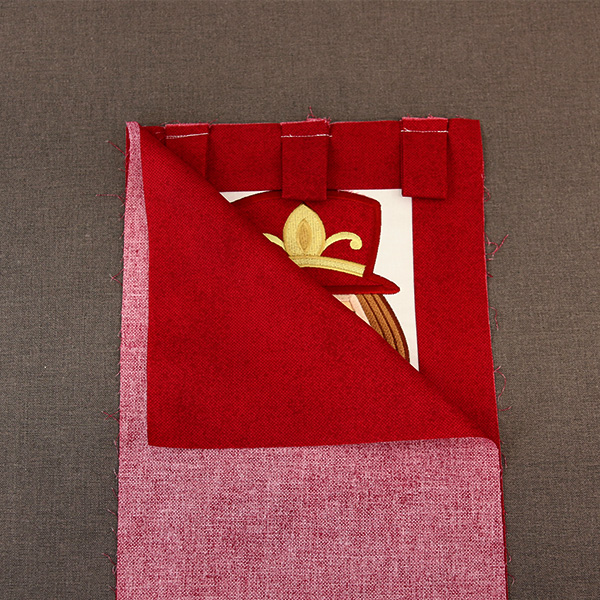
To make the back piece, measure your whole panel scene including the outer borders. For example ours measured to 27in x 9.5in.
Then cut out a single piece of fabric to those same measurement to create the back piece. We cut our back piece out of the same fabric we used for the outer borders.
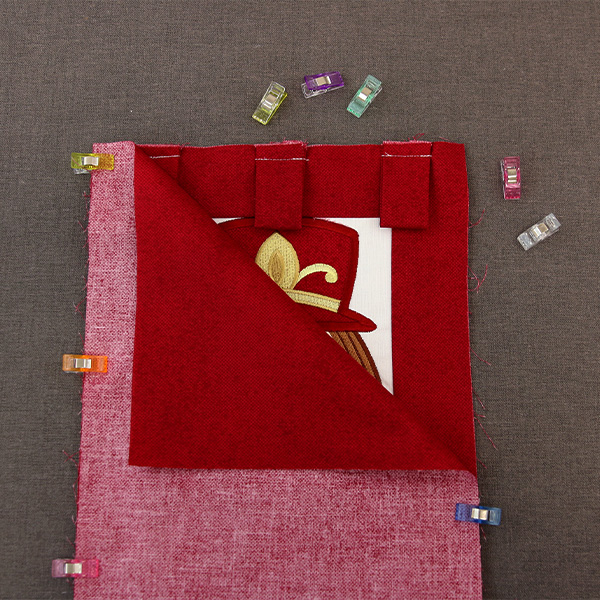
Lay the back piece on top of the front panel scene piece with right sides together. Then pin or clip the pieces together along all four sides.
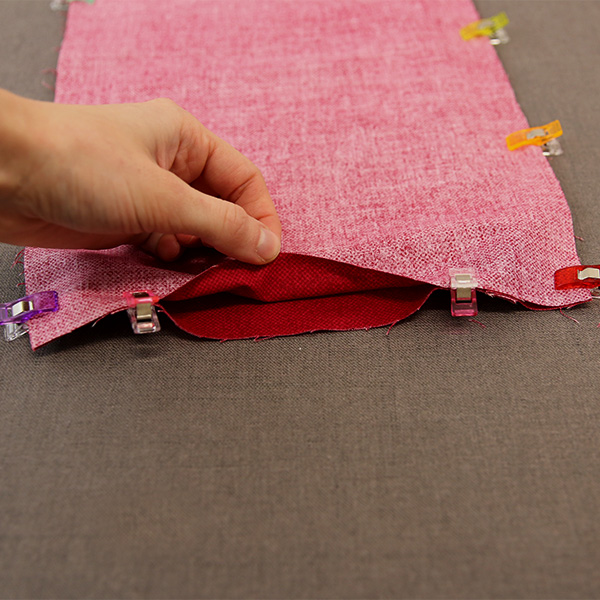
Make sure to leave at least a 6in opening at the bottom edge of the panel scene while pinning and sewing in the next step. This opening will allow you to turn the panel scene right side out after sewing the front and back together.

Sew around the four outside edges using the same seam allowance that you used when making the outer border measurements. We used a 1/2in seam allowance. Remember to leave at least a 6in opening along the bottom edge.
Once you have finished sewing, clip off the corners to remove excess bulk. Be careful not to cut the stitching. This will help the corners lay flat when it's turned right side out.
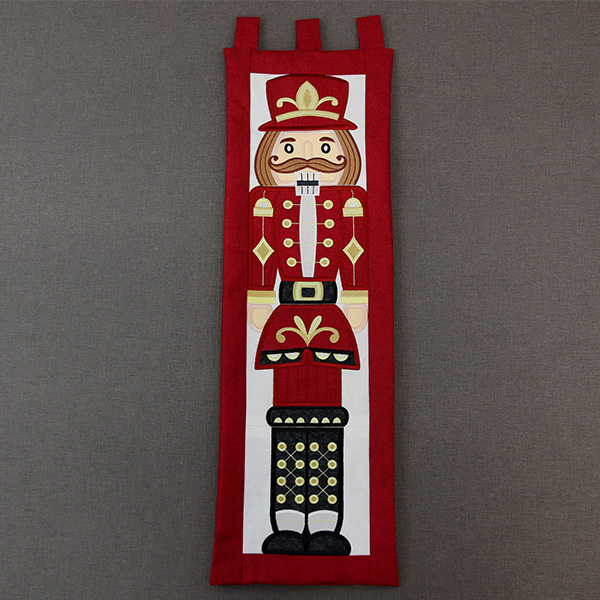
Reach into the opening, and turn the whole panel scene right side out.
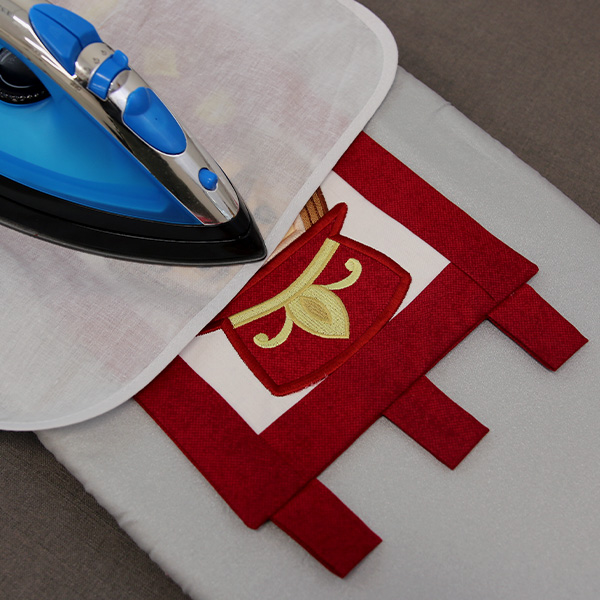
After the panel scene is right side out, use an iron and pressing cloth to press all the edges. Carefully fold in the edges of the opening your seam allowance amount, and press the edges.
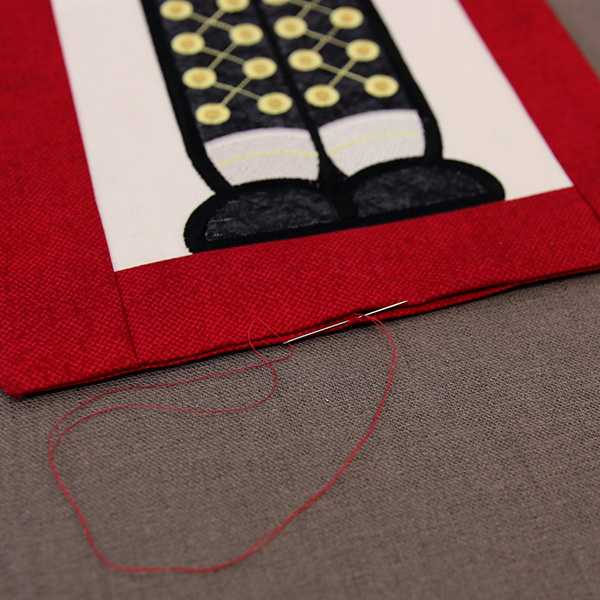
Using a hand sewing needle and thread, sew the opening closed along the bottom edge. Make sure to keep the raw edge of the fabric folded inside the panel scene as you sew.
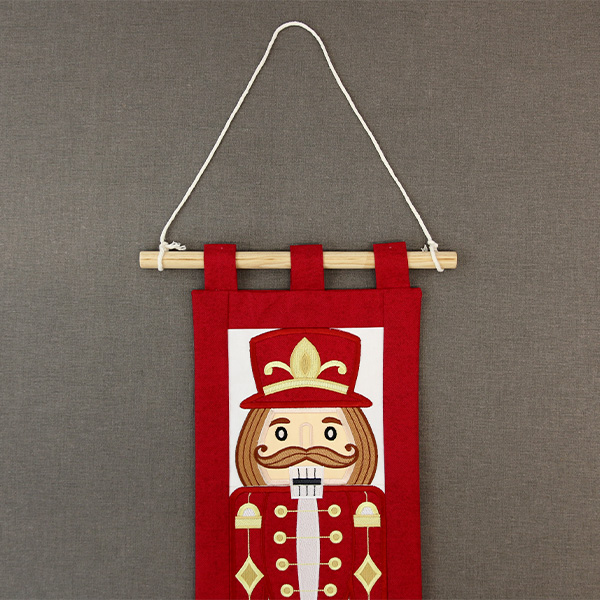
Slide a wooden dowel through the three hanging loops, and use your preferred method to hang the panel scene. In this example we used cord cut to 30in long and tied it to either end of the dowel.
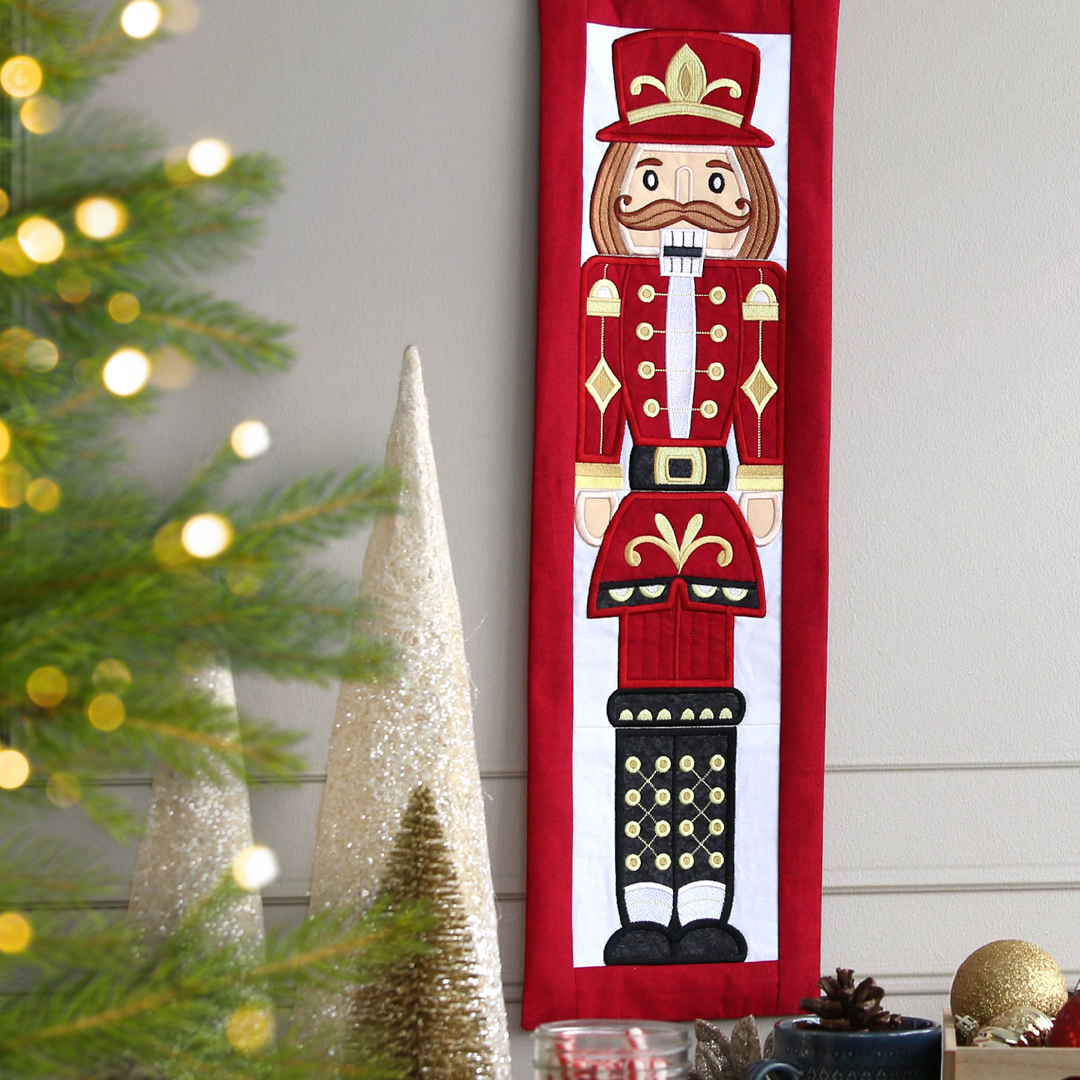
Now that the Applique Panel Scene is completed, display it in your home to add some homemade charm, or give it as a beautiful gift.